自動車・輸送機器メーカー 大手自動車メーカーA社様
導入ポイント
-
課題●工場の電力消費データを計測し、改善策によって削減につなげたい
●以前からデータは取得していたが社内での加工に時間と負荷がかかっていた -
評価ポイント●電力消費データ収集からアウトプットまでシステム開発を担える総合力
●グラフ作成の自動化で内部作業のアウトソーシングを実現できる -
効果●各工程の電力消費をリアルタイムで表示、異常値発生時の即応が可能に
●W e b 化によって、工場間のデータ共有が実現し、相互支援体制が整う
課題
工場の消費エネルギーを“変える”と“減らす”で削減
眠っていたデータを新たなシステム導入で呼び覚ます
大手自動車メーカーA社では、国内外に数多くの工場を展開し、生産台数では世界屈指の規模を誇っています。そうした中、近年、世界的に重要なテーマとなっているのが、環境問題への対応です。A社では、自動車自体の環境負荷の低減を図ると同時に、工場内で太陽光や風力など再生可能エネルギーを導入。一方で、製造工程で使用するエネルギー自体を削減することも目指しています。こうして、再生可能エネルギーに“変える”と、使うエネルギー量自体を“減らす”両面作戦も駆使して、CO2総排出量を大幅削減することを目標に、施策を推進しています。
そして、A社の生産本部が現在力を入れて挑もうとしているのが、後者の「使うエネルギーを減らす」施策です。既にいくつかの工場では、製造現場の電力消費量の計測を行っています。「しかし、データは蓄積されるものの、有効に使われていないケースが大半。導入したシステムが実質的には“眠っていた”わけです。また、使っている場合でも、データのグラフ化などの加工は社内の担当者が行い、データを受け取ってから計算ソフトで作成するのに時間がかかり、負担にもなっていました」(A社システム担当者K氏)。
一方で、生産本部の他のチームが、BI分析プラットフォームの「Tableau」を活用し、国内外にある各工場の「生産台数」をリアルタイムに表示するシステムを先行して導入。「Tableauを使ってその“エネルギー版”ができないか」と同K氏は考え、今回の新たな電力消費計測システムの導入プロジェクトがスタートしたのです。
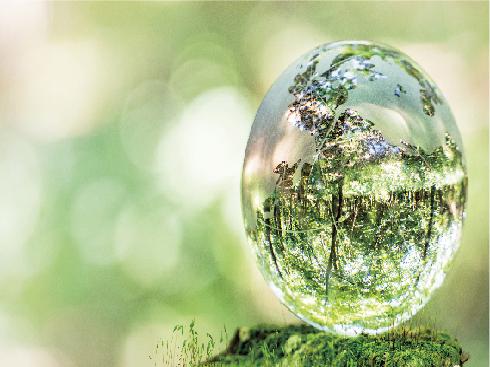
評価
シンプルな仕組みだがロジックの構築が難題
クオリカの知見、実績、総合力でハードルを越える
導入にあたり、A社では複数のシステムベンダーに声をかけ、実現の可能性を検討。その中で、いち早く手を挙げたのがクオリカです。Tableauを活用し、設置された電力量計から集まるデータをグラフ化するアウトプットまで、全てのシステム開発を一手に担えるクオリカの総合力の高さを評価し、A社のシステム担当者は採用を決断したのです。
具体的なシステム概要は次の通りです。まず、工場の生産ラインの各工程に電力量計を設置。そこで計測されたデータはリアルタイムに閉域網経由でデータベース(DB)に蓄積されます。そのデータをTableauによってグラフ化して表示する仕組みです。「シンプルなシステムで一見作るのが容易に思えますが、ロジックがしっかり構築されていないと、うまくデータが流れない。実は難易度が高い開発」(同K氏)。その点、クオリカはインフラからソフトウェア開発まで様々なサービスを展開しており、システム間のデータ連携を図る知見と実績、技術力で一歩リードしていました。「特にTableauによるアウトプットも含めて自動化できる開発力が大きなポイントだった」と、同K氏は振り返ります。
グラフ化されたデータは、Webシステムを導入することによってクラウドサービス経由で、全ての関係者がいつでもどこでもアクセスして見ることができるようになりました。こうして、スタート時に導入された国内3工場では、生産ラインの様々な工程ごとに電力消費量を計測、自動表示できる“見える化”が実現したのです。
効果
本部と各工場がリアルタイムで電力消費データを共有
工場間の違いの議論や問題発生時の相互支援を模索
クオリカが作成した画面では、「年次(毎月の推移)」、「月次(毎日の推移)」「週次(曜日ごとの推移)」「日次(毎時の推移)」の4つのグラフを並列で同時に確認することができます。本システムの最も有効なポイントは、関係者が“リアルタイム”でデータをチェックできる点です。「もし異常値が見つかれば、その場で現場に確認に行って原因を探り、必要に応じて即時に電力を削減する対策を打つことができます。これが、データを見える化するまでに時間がかかっていた従来のシステムとの違いです」(同K氏)。
さらに、優れているのは、関係者全員がリアルタイムデータを“共有”できる点です。例えば、3工場のうち1工場で問題が発生した場合、他の2工場の関係者がデータを見ながら改善のための助言を与えることが可能。あるいは、1工場の電力削減のベストプラクティスを他の2工場の関係者に展開することも容易です。同じ部品を作っているのに、電力消費量が高い工場と低い工場があれば、違いを議論して改善につなげることもできます。「以前は電力量のデータを工場間で共有することはなかった。本システムで互いに切磋琢磨できる環境が整った」と、同K氏は言います。
ただし、すぐに自社工場でデータを活用したり、共有して工場間のコミュニケーションを活発化させることは、ハードルが高いと認識。そこで、最初は生産本部が中心となり、データの分析や対策を立てるための支援を行っていく計画です。例としては、現状の自動車1台当たりの生産にかかる電力消費量を計測し、それを下回る目標値を決めて、工程ごとに削減の可能性を検討するなど。「課題を設定して、PDCAを回していく中で改善策を探っていきたい」と、同K氏は話します。
年次、月次、週次、日次の4つのグラフはデフォルトで用意したもので、現場からの要請があれば、他の切口に変更することも可能です。そこは、クオリカのエンジニアが臨機応変に対応し、現場にとって最も必要なリアルタイムデータを提供していきます。
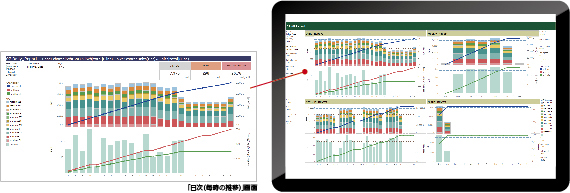
今後の展開
データ作成の自動化を外部委託し、コア業務に集中
消費エネルギーは全て“リアルタイム見える化”が可能
社内の人的リソースが限られる中、データを加工することに人手を奪われ、対策を考えるコア業務に集中できない企業も多いでしょう。今回紹介した大手自動車メーカーA社は、データを作る部分までをクオリカに外部委託することで、少数精鋭で現場の改善に力を注げる体制を整えたのです。
今後は3工場で効果を検証し、その結果に応じて、自動車以外の他の製品にも広げていくことを視野に入れています。さらに、国内やグローバルに横展開することも模索しており、そうした場合、クオリカが拡張プロジェクトを全面的にバックアップしていきます。
また、計測する対象を増やすことも可能。自動車工場でいえば、圧縮エア、ガスなど他のエネルギーの自動測定・グラフ化もできます。工場で消費するエネルギーは、クオリカがセンサーとネットワーク、DB、BIツールを組み合わせて構築することによって、全て“リアルタイムの見える化”が可能なのです。「将来的には、各工場から自主的な提案が次々と挙がり、全体のエネルギー削減につながる体制を作りたい」と、同K氏は期待を寄せています。
お客様のプロフィール
- 会社名
- 大手自動車メーカーA社
- 事業内容
- 輸送用機器(四輪車、汎用製品など)の研究・開発・製造を手掛ける。国内とグローバルに複数の生産工場を展開。
お問い合わせ先:MA第二事業部
TEL:03-5937-0750
FAX:03-5937-0802